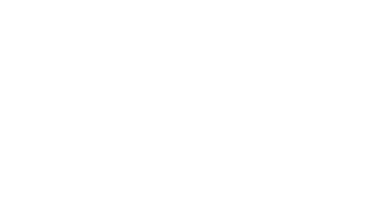
These days the concepts of “supply chain risk management” and “resilient supply chain” are trending more than ever before. At the same time, companies may or may not have plans for risk management, business continuity or even simple contingency plans to mitigate the impact of external events on their businesses – events such as the current pandemic. In any case, in the coming months one item will certainly be on the agenda of operations managers and supply chain managers alike: Rethink the Supply Chain.
But we can’t talk about the supply chain, without addressing supply chain risk, and risk in general.
In any given organization, we can classify risk into three categories: internal, supply chain, and external. Internal risks can be further divided into risks linked to operations or management decisions. Instead supply chain risks derive from relationships with business partners, which are also divisible in two subsets: risks associated with suppliers or with customers. Last come external risks (natural phenomena, pandemics, tariff policies, changes to legislation or regulations, and so forth). Of course, individual companies are powerless to mitigate the chances that these events occur, but they can certainly action certain levers to minimize the subsequent impact.
What we’ve been experiencing in recent weeks days is clearly an external phenomenon which will have huge repercussions on the supply chain and on internal activities. But the response by companies may be limited to protecting themselves in the current contingency, without going any further and totally rethinking their supply chains, managerial processes, and support systems from a risk-agnostic perspective. If this is the case, then we have learned nothing from this experience. Today’s problem is a pandemic, and yes it is a dramatic one. But tomorrow’s might be an earthquake. The next day it will be tariffs, and the day after that the cost of crude oil will hit 100 euro a barrel.
So company supply chains have to be resilient in the face of any contingency. Simply put, we can say that to achieve this resiliency, we essentially need to strive for two objectives: visibility and agility. But unfortunately these must be balanced with a third, which is - as always - cost efficiency. What we often forget is that hitting the first two targets will generate a cost. It’s easy to say that we want to know all our suppliers, be they first, second or third level – but this has a cost.
Rethinking the supply chain to enhance visibility and agility, as I see it, means taking a synergistic approach to these four areas: supply chain design, supply chain planning & control, supplier relationship management and distribution channel & assortment planning. It’s very likely that some of the actions described below are already on the agenda for some companies and managers. But I think the coronavirus emergency will make them top priority.
As far as supply chain design, the first essential step is to rethink the supply network in terms of the locations of plants and suppliers. Companies have to figure out how to balance local, regional, and global suppliers to achieve greater agility and raise the visibility of upstream processes. Second comes reconsidering make or buy decisions, or perhaps we should say make and/or buy decisions. In this respect, companies should to identify which activities, production processes, and components to handle internally, or externally (in this case minimizing single sourcing) or both. The aim here is to prevent a loss of knowhow on critical products, materials, and technologies. Last, it’s important to reassess the distribution network and the logistic strategy, taking into account the number, role, and location of warehouses, as well as transportation and customer delivery services. This while keeping in mind that the demand mix related to products - and more importantly markets and sales channels - could radically change moving forward, with respect to what we’re used to.
Moving on to supply chain planning & control, processes for Sales & Operations Planning (S&OP) and relative support systems should be introduced or retooled. Big players in several B2C industries (such as food & beverage, automotive, pharma, consumer electronics, and household appliances) have already been investing in these processes over time. But they are virtually non-existent in other B2Cs (like fashion), in almost all B2B sectors, and among medium-sized industrial concerns in general. All too often managers are focusing on planning for what will happen next week, while spending too much time trouble shooting. Rarely do they dedicate their time to looking at the big picture in the medium term. So these processes must become strategic, evolving toward the concept of Integrated Business Planning (IBP).
What’s more, planning processes have to encompass two more aspects: an economic and financial view of supply chain planning and a transition from the concept of one number to scenario planning, which allows companies to make a rapid appraisal of the impact of various supply chain scenarios. Also indispensable is rethinking the approach to stock management following two streams: one, utilizing self-adapting inventory control systems for monitoring surplus levels along the supply chain (with far faster and more frequent recalculations of planning parameters for finished products, components, and raw materials), and two, introducing the idea of establishing a strategic surplus to counter potential risk rather than to meet operational parameters.
What also emerges in the current context is the opportunity to move to a system based on a collaborative and vertical approach, (i.e. upstream with suppliers and downstream with customers), as well as horizontal one (working with companies in the same sector and in the same district). The last essential component is a supply chain control tower which serves to provide visibility along the supply chain from end to end. The capacity to quickly re-plan the supply chain inevitably means activating sensors that make it possible to monitor the flow of materials and products in a rapid, reliable way.
Now we come to supplier relationship management, where there are four points that organizations should focus on. The first is shoring up processes for qualifying, auditing and vendor rating suppliers. Some variables to consider here are location, financial robustness, environmental and social responsibility, managerial competency, the propensity for collaboration and/or innovation - all of which cannot be reduced to a simple assessment of costs, service and quality. It’s likely that companies will raise the bar in evaluating and qualifying suppliers, while at the same time, cultivating long-term relationships based on trust. The second point has to do with enhancing visibility along the supply chain not only of first level suppliers, but second and third level too. The aim here is to minimize not only the risk of disruption, but other risks as well: environmental, social, security, etc. The third point relates to rethinking the rationale and the provisions of supply contracts (with an eye to finding the right tradeoff between coverage and flexibility). The fourth and final point ties into the use of tools for Supply Chain Finance, that is, solutions that allow companies to fund their own working capital.
In terms of distribution channel & assortment planning, it’s undeniable that the current emergency has accelerated the speed with which e-commerce channels have sprung up to support traditional channels. This calls for revamping logistical processes of warehousing and transportation, pinpointing the proper degree of convergence and the optimal tradeoff between costs and services. Lastly, as regards the product portfolio, processes of assortment streamlining will probably be triggered, which will lead to a supply chain overhaul both in terms of design and planning.
In conclusion, the coronavirus must force us to rethink the supply chain, taking a far more strategic approach. To do so, companies could conceivably follow a three-stage route. First they should embrace (share and internalize) this approach at an executive level, adapting it to the specificities of their sector, and above all, of their individual companies. Then, as with any process of change, organizations must make a differential assessment with respect to the existing model, and then map out a path to change. Lastly, companies need to make the move to action through progressive consolidation, putting each piece of the puzzle in place, one at a time. Because agility is not just an aim to be achieved; it’s something that must always be present, every step along the path to change.
To achieve all this, skills are a must (both internal and external), as well as enabling systems and technologies. The question is: Will companies have the capacity and the courage to invest time and money in this change?