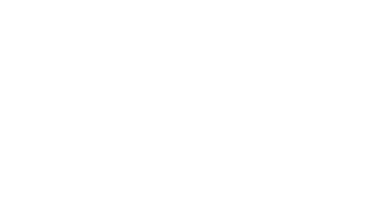
- Data inizio
- Duration
- Format
- Language
- 17 sep 2025
- 4,5 days
- Class
- Italian
Apprendere metodi e capacità di intervento organizzativo per adeguare la struttura aziendale alle attuali esigenze di fluidità e flessibilità di assetti e funzioni.
To what extent have Industry 4.0 technologies been adopted in Italy to pursue specific production strategies in manufacturing? And with what results? Although new tools do not appear to contribute significantly to improving environmental sustainability, they are enablers for other strategies that can lead to notable results.
“Industry 4.0,” a term originally coined in Germany, became a buzzword in 2011 thanks to that country’s government. It refers to the Fourth Industrial Revolution triggered by the dissemination of digital technologies. Industry 4.0 represents a turning point for European manufacturing production, which explains the support from the EU within the framework of a broader strategy to promote a digital single market by funding research and infrastructure development.
It is truly a revolution destined to affect millions of companies through specific initiatives.
To encourage the adoption of an Industry 4.0 approach, in late 2016 Italy’s Ministry of the Economy launched the “National Industry 4.0 Plan,” a roadmap financed by the government to provide incentives to companies to invest in and upgrade existing technologies. According to data from the Italian Ministry of Economic Development, at year’s end 2017, 8.4% of Italian companies had implemented Industry 4.0 technologies, and an additional 4.7% had planned to develop these tools in the next three years. In 2017, thanks to the government’s plan, investments scaled up by 11% over the previous year, a figure that rose to 13% in the machinery and equipment sectors.
Companies get the biggest value out of Industry 4.0 when it serves to reinforce and renew their business model. Indeed, to achieve long-lasting improvement by riding the new wave of innovation, companies not only need to identify strategic objectives, but also pinpoint the most appropriate manufacturing strategy to pursue.
The strategic trends emerging in the field of operations management, which seem to be closely linked to the adoption of Industry 4.0 technologies, can be categorized as follows: production assistance, outsourcing and supply chain management, digitalization of operations, and adopting common lean methodologies.
The aim of our recent study was to understand the extent to which Industry 4.0 technologies have been adopted in the context of Italian manufacturing companies. We also wanted to verify whether or not these technologies were being leveraged to pursue specific manufacturing strategies.
Our findings offer useful insights for researchers and practitioners alike to analyze and unpack the type of benefits that can come from Industry 4.0 solutions, and to explore the main areas of interest where these technologies can be deployed.
The questionnaire we designed for our study is made up of three sections. The first has questions that serve to get descriptive information on respondents and the companies they work for. The second contains six questions that assess the impact of Industry 4.0 technologies on the pursuit of strategic corporate objectives (in the opinion of respondents). The third section includes seven questions that aim to ascertain whether the companies have actually adopted Industry 4.0 technologies (or are planning to do so).
To frame the statistical data, which we obtained by administering 200 questionnaires, we asked interviewees to freely express their opinions on the challenges and obstacles they’ve encountered. In each section of the questionnaire, in fact, there was space for open answers, where interviewees had the chance to add their feedback in the form of suggestions and notes.
From our preliminary work, including a literature review of the sector, we found the six most common and influential strategies among the 200 companies in our sample: 1. Servitization and integration with customers 2. Supply chain integration 3. Integration of machinery, electronic equipment and databases 4. Lean & Agile systems 5. Sustainable production and logistics (Green) 6. Design-to-Cost
Then we identified seven technologies as enablers of these strategies: digital supply chain, cloud, IoT, robotics, Big Data, additive 3D, and vehicles.
Our quantitative findings clearly show that only a minority of the organizations in our sample shows no interest at all in Industry 4.0 (37.4%). In contrast, 25.6% of sampled companies are considering adopting these technologies; 18.9% are already realizing projects that incorporate Industry 4.0; and 18.1% have already completed a series of initiatives integrating Industry 4.0 into their business.
Both quantitative and qualitative results reveal that five out of the six strategies are currently being implemented by the companies in our sample in one or more projects, with the only exception being Green. Design-to-Cost seems to be widely consolidated, and actioned specifically by new technologies for virtualization and simulation, such as 3D printing.
As for integration of both supply chains, as well as machinery, electronic equipment and databases, all this is supported by a cluster of technologies that include IoT, robotics and the cloud. Servitization can be achieved through customer integration processes thanks to the cloud and big data. And lastly, the lean strategy can also leverage Industry 4.0 solutions for deployment, despite the fact that in their qualitative comments, interviewees expressed a range of concerns about the compatibility of automation with the dynamics of lean environments (where the workplace and the layout can change on a daily basis).